Advanced Production Planning and Scheduling oder (APS)-Lösungen, die auf künstlicher Intelligenz und digitalen Zwillingen basieren, steigern die Produktivität und Flexibilität erheblich und ermöglichen eine effiziente Vorbereitung und Reaktion auf Arbeitskräftemangel und Unsicherheiten in den Lieferketten. Leider sind sich die meisten Unternehmen nicht der Probleme bewusst, die bei der Implementierung dieser Lösungen auf sie lauern.
Die Produktion steht ständig unter dem paradoxen Druck, gleichzeitig die Bestände zu reduzieren und die Durchlaufzeiten zu verkürzen. Die Rahmenbedingungen für Fertigungsunternehmen werden durch die Forderung nach höherer Produktivität und Flexibilität, sowie nach kleineren Produktserien und kürzerer Produktlebensdauer weiter verschärft.
Drei Mitarbeiter in einem Unternehmen sind die ganze Zeit in der Brandbekämpfung gebunden!
Trotz der zunehmend unsicheren Marktbedingungen setzen sich die Unternehmen mit Engpässen, Ausfällen und Verspätungen nach wie vor eher laufend oder nur dann, wenn sie schon auftreten, auseinander. Im Durchschnitt sind also drei Personen in einem Unternehmen in Vollzeit mit der Brandbekämpfung beschäftigt! Während schnelle Reaktionen und Korrekturen den Schaden durch unerwartete Ereignisse in der Produktion verringern können, wächst die Notwendigkeit, diese zu antizipieren und sich darauf vorzubereiten.
Einmal längere Einführungszeit
Unternehmen, die zu den Vorreitern der digitalen Transformation gehören, beschleunigen daher ihre Einführung von APS-Lösungen. Wir stellen jedoch häufig fest, dass die Anwender beim Testen verschiedener Funktionalitäten enttäuscht feststellen, dass diese Lösungen nicht funktionieren, weil die damit erstellten Produktionspläne völlig unrealistisch sind! Verzögerungen bei der Umsetzung, die je nach Größe des Unternehmens im Durchschnitt sechs bis 12 Monate dauern, führen weiterhin zu einer schlechten Akzeptanz. Dabei zeigen die Marktdaten, dass dieser Zeitraum in der Regel noch länger ist!
Wenn wir einen Schritt zurückgehen, können wir auf der Grundlage unserer Erfahrung aus mehr als 30 erfolgreichen Implementierungen von APS-Lösungen in der CEE- und DACH-Region die Hauptgründe dafür identifizieren, warum bis zur Hälfte der APS-Projekte scheitern.
Wichtige Mitglieder des Projektteams und ihre ständige Präsenz
Zuallererst müssen sowohl der Anwender als auch der Anbieter von APS-Lösungen einen ausgezeichneten Projektmanager einsetzen und einen Hauptanwender bestimmen, der in der Regel ein recht erfahrener Produktionsplaner ist. Darüber hinaus muss für alle wichtigen Projektmitarbeiter eine ständige Anwesenheit oder eine angemessene Vertretung bei Abreise oder längerer Abwesenheit gewährleistet sein.
Klarer Überblick über das Angebot und die zu erbringenden Leistungen
Im nächsten Schritt müssen der Nutzer und der Lösungsanbieter ihre Erwartungen sehr gut aufeinander abstimmen. Ein klares und gegenseitiges Verständnis aller angebotenen Produkte und der erwarteten Ergebnisse und Funktionen ist wirklich entscheidend! In diesem Zusammenhang kann ein Referenzbesuch in einem anderen Unternehmen, welches bereits Erfahrungen in der Einführung eines APS – Systems gemacht hat, sehr nützlich sein.
Zeitplan, Fabrikinventar und Prozesse
Zu den wichtigsten vorbereitenden Schritten für eine erfolgreiche Implementierung gehören die Erstellung eines Zeitplans, die Erstellung eines Blueprints oder einer Bestandsaufnahme der Fabrik und die klare Definition und Konsolidierung aller wichtigen Arbeitsabläufe. Dabei geht es insbesondere um die Erfassung von Stammdaten, organisatorische Änderungen und Anpassungen der Arbeitsabläufe im Unternehmen. In diesem Schritt sollte sowohl die Geschäfts- als auch die Betriebs- und/oder Produktionsebene des Unternehmens, einschließlich der IT-Abteilung, eingebunden werden.
Schwierige Konsolidierung
Die Konsolidierung aller wichtigen Arbeitsprozesse ist oft am schwierigsten, da die Fähigkeiten und Kompetenzen innerhalb eines Unternehmens zur Implementierung einer APS-Lösung verteilt sind. Einige Unternehmen wollen nicht so tief in diesen Bereich eindringen. Diejenigen, die schon einmal diesen Fehler gemacht haben, wissen aber, dass dies ein entscheidender Schritt ist, da sonst schnell eine ganze Reihe von organisatorischen, informationstechnischen und strategischen Problemen auftauchen können.
Bearbeitung und Pflege von Stammdaten
Leider ist es in der Praxis auch oft so, dass die Benutzer immer mehr Funktionen hinzufügen wollen, anstatt eine gute Basis für die Lösung zu schaffen, die sie implementieren möchten. Ein sehr wichtiger, wenn nicht sogar der kritischste Faktor für den Erfolg jeder APS-Implementierung ist die Verwaltung und Pflege von Stammdaten. Dabei handelt es sich hauptsächlich um Normen, technologische Verfahren, Einstellungen, Matrizen zur Aufgabenverteilung, sowie unterschiedliche Produktionsversionen. Auch müssen den Änderungen Rechnung getragen werden – Unternehmen führen neue Produkte und Produktlinien ein, verbessern technologische Prozesse, etc. All das muss regelmäßig in das ERP-System eingegeben und gepflegt werden. Das Hindernis, das dem meist entgegensteht, ist der Mangel an Personal.
Die Lücke zwischen Planungstheorie und Produktionsrealität
Einer der Faktoren, an denen die Umsetzung von APS-Lösungen scheitert, ist die Kluft zwischen Theorie und Praxis. Selbst wenn in einem Unternehmen die Stammdaten gepflegt sind und es beginnt, mit einer neuen APS-Lösung Pläne und Mikropläne zu erstellen und diese dann mit der Realität abgleicht, wird es feststellen, dass noch Korrekturen und Anpassungen vorgenommen werden müssen. Das liegt oft daran, dass Stammdaten von der Technologie festgelegt werden, die wiederum auf der Grundlage von Theorie und Erfahrung zum Zeitpunkt der Entwicklung festgelegt wurden. Diese Daten sind in der Regel nicht im ERP-System nachgepflegt worden und spiegeln sie nicht die tatsächliche Situation wider.
Dies ist in der Regel auf eine zu große Anzahl von Produkten zurückzuführen, deren Analyse und Pflege zu viel Zeit in Anspruch nehmen würde. Infolgedessen können die Zeiten und Produktionspläne, die sich aus diesen Daten ergeben, von der Realität abweichen.
Was können Unternehmen also tun, um Unmut, Zeit- und Geldverschwendung und Misstrauen gegenüber modernen Technologien zu vermeiden? Vor allem muss vermieden werden, dass die Personen, die das Projekt zur Implementierung von APS-Lösungen geleitet haben, entlassen werden.
Vorschläge und Lösungen für eine erfolgreiche Implementierung von APS-Lösungen
Um die Erfahrungen unserer Anwender und die Rückmeldungen anderer Unternehmen zusammenzufassen, ist es also wichtig, sich zunächst mit dem Anbieter abzustimmen, damit beide Parteien das gleiche Verständnis von dem haben, was angeboten wird. Um das Projekt umzusetzen, müssen die Unternehmen für eine ausreichende Personaldecke sorgen und ihre digitalen Kompetenzen sowohl auf Management- als auch auf operativer Ebene aktiv ausbauen. Vor allem müssen sie auf Veränderungen und Verbesserungen der Arbeitsabläufe und -prozesse sowie auf mögliche Unstimmigkeiten auf allen Ebenen vorbereitet sein.
Wie künstliche Intelligenz und der digitale Zwilling helfen
Auf dieser Stelle können wir nicht genug betonen, dass ein Unternehmen dringend eine Person braucht, die sich Vollzeit um die Pflege der Stammdaten kümmert! Wenn man weiß, dass dies eine Herausforderung ist, macht es umso mehr Sinn, Lösungen einzusetzen, die auf den neuesten KI- und digitale Zwillings -Technologien basieren. Der digitale Zwilling der Fabrik lernt ständig und arbeitet mit realen Produktionsdaten, die er dem Benutzer anzeigt und im ERP-System pflegt.
Garantierte Rückmeldung
Ein weiterer Vorteil von KI-basierten APS-Lösungen besteht darin, dass sie sowohl Planer als auch Teamleiter dazu bringen, ein und das gleiche Werkzeug zu verwenden. Dadurch wird vermieden, dass die APS-Lösung einen Plan erstellt, der als Tabellenkalkulation in die Produktion geht, wobei man keine garantierte Rückmeldung für das erhält, was tatsächlich in der Produktion passiert. Für Produktionsplaner ist es äußerst nützlich, nicht nur die Probleme in der Produktion zu erkennen, sondern auch die Auswirkungen des Problems, sowohl auf den Produktionsplan als auch auf die tatsächliche Realisierung, indem unerwartete Ereignisse vorhergesagt werden können.
Planungstheorie und Produktionsrealität kombiniert
Sobald eine APS-Lösung die Theorie der Planung mit der Realität von Produktionsanlagen verbindet, werden Produktionspläne und Mikropläne viel realistischer, Unternehmen sparen Zeit bei der Erstellung von Plänen und können viel effektiver auf unerwartete Komplikationen reagieren, bevor es zu Engpässen oder Stillständen kommt.
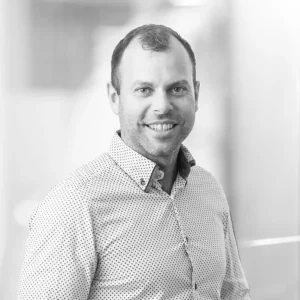
Gregor Sablič
CSO at QLECTOR